In construction, concrete drying is a crucial aspect that significantly impacts a project’s longevity and structural integrity. Understanding how long concrete takes to dry is paramount for builders and contractors seeking optimal results. In this blog, we delve into the definition of concrete drying, highlighting its importance in ensuring the success of construction endeavours. Additionally, we’ll provide an insightful overview of the diverse factors that influence concrete drying time. Join us as we unravel the intricacies of this fundamental stage in construction, where time is not merely a measure but a key determinant of success.
Table of Contents
Understanding Concrete Drying
Concrete drying is a pivotal phase in construction, demanding a nuanced understanding for successful project outcomes. Beyond the surface, the intricate drying science involves chemical reactions, careful consideration of water-cement ratios, and the delicate balance between curing and drying. Let’s delve into the fascinating realm of understanding concrete drying to appreciate its complexities and implications.
The Distinction Between Curing and Drying
Concrete curing and drying are often used interchangeably but are distinct processes. While curing involves maintaining adequate moisture for chemical reactions, drying marks eliminate excess water. Clarifying this difference is essential to comprehend the holistic picture of concrete development.
Chemical Reactions at Play
Concrete drying is not merely the evaporation of water; it’s a chemical journey. The hydration process, where water reacts with cement, contributes to strength development. Understanding these reactions shows why proper drying is critical for achieving optimal concrete strength and durability.
Significance of Water-to-Cement Ratio
The water-to-cement ratio is a fundamental factor influencing concrete drying. Striking the right balance is imperative, as excess water can prolong drying time, potentially compromising the concrete’s structural integrity. We explore the science behind this ratio and its impact on drying.
Variables Influencing Concrete Drying Time
Ambient conditions such as temperature, humidity, and wind play a pivotal role. Concrete mix design, surface area, and thickness further contribute to the intricacies of drying time. Unravelling these variables equips builders with the knowledge to navigate and control the drying process effectively.
Monitoring Techniques
Accurate monitoring is essential throughout the drying process. Moisture meters, relative humidity testing, and regular inspections enable builders to make informed decisions, ensuring that the concrete evolves in alignment with project requirements.
Understanding concrete drying is akin to deciphering a complex code that, when mastered, ensures the solid foundation of any construction project. With this knowledge, builders can navigate the nuances of drying times, optimize strength, and lay the groundwork for structures that stand the test of time.
Factors Influencing Concrete Drying Time
When it comes to concrete construction, the drying time of the material is a critical factor that demands meticulous consideration. Several elements contribute to the speed and efficiency of concrete drying, influencing the overall success of a construction project. Let’s delve into the key factors that play a pivotal role in determining how long it takes for concrete to dry:
- Ambient Conditions: Concrete drying rates are impacted by temperature, humidity, and wind speed. Elevated temperatures hasten the process, but high humidity can extend it. Efficient air circulation facilitates faster drying. Balancing these factors is crucial for optimizing concrete curing times and ensuring the durability and strength of the final structure.
- Concrete Mix Design: Maintaining an optimal water-to-cement ratio is paramount in concrete mixing. A higher ratio prolongs drying, impacting final strength. Additives such as accelerators haveten curing, while retarders extend the process. The delicate balance ensures the concrete attains the desired durability and performance characteristics during and after setting.
- Surface Area and Thickness: A greater surface area expedites the drying process of concrete, as increased exposure facilitates faster moisture evaporation. Conversely, thicker concrete components necessitate more time for drying, as the moisture dissipates gradually from the surface. The interplay between surface area and thickness significantly influences the overall drying time of concrete structures.
- Use of Accelerators or Retarders: Accelerators hasten concrete curing in cold climates or time-critical endeavours, ensuring swift completion. Retarders, conversely, decelerate drying, accommodating intricate work or adjustments. These additives empower precise control over concrete setting times, optimizing construction processes based on environmental conditions and project intricacies.
Understanding these factors empowers builders and contractors to make informed decisions, ensuring that concrete drying aligns with project timelines and quality standards. By navigating the intricate interplay of these elements, construction professionals can optimize the drying process and lay a solid foundation for successful and durable structures.
Tools And Instruments For Monitoring Drying
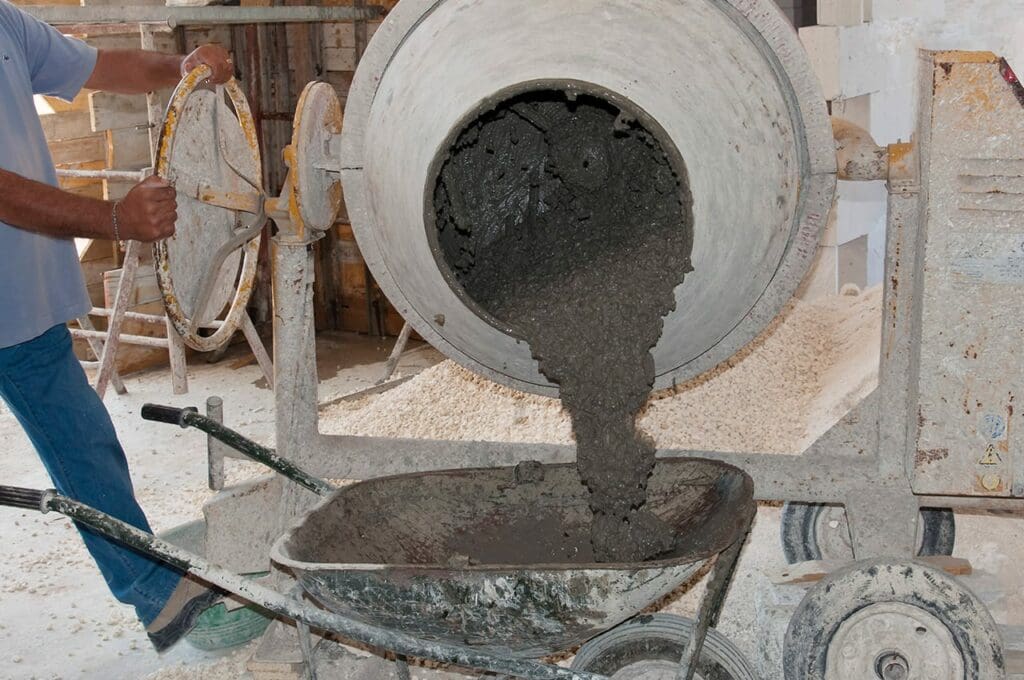
Ensuring that the drying process proceeds as planned in concrete construction is essential for achieving structural integrity and durability. Various tools and instruments have been developed to monitor the drying progress accurately. This article explores some of the critical tools construction professionals use to assess and manage concrete drying.
Moisture Meters
Moisture meters are indispensable tools for gauging the moisture content within concrete. By providing real-time readings, these handheld devices offer quick and efficient assessments, allowing contractors to make informed decisions about the readiness of concrete surfaces for the next phase of construction.
Relative Humidity (RH) Testing
RH testing involves placing sensors within the concrete to measure the relative humidity levels. This method offers a comprehensive understanding of the moisture conditions deep within the concrete, guiding construction teams on when it is safe to proceed with subsequent construction tasks.
Surface Thermometers
Surface thermometers are utilized to measure the temperature of the concrete surface. As temperature plays a crucial role in drying, these tools ensure that environmental conditions align with optimal drying parameters.
Infrared Cameras
Infrared cameras are valuable for detecting variations in temperature across the concrete surface. By identifying potential cold or damp spots, construction professionals can address specific areas that may require additional attention or time for drying.
Data Loggers
Data loggers continuously monitor and record environmental conditions such as temperature and humidity over time. This historical data is valuable for analyzing trends and adjusting the construction schedule based on past drying performance.
Concrete Conductance Meters
Conductance meters measure the electrical conductivity of concrete, providing insights into its moisture content. This non-destructive testing method aids in determining whether the concrete has reached the desired dryness level for subsequent construction activities.
Calcium Chloride Testing
Calcium chloride testing involves placing sealed containers of calcium chloride on the concrete surface to measure the rate of moisture vapour transmission. This method is commonly employed to assess the drying conditions of concrete in various applications.
The tools and instruments mentioned above are instrumental in meticulously monitoring concrete drying. Employing these technologies empowers construction professionals to make informed decisions, ensuring that concrete reaches the desired dryness level before advancing to the following stages of construction. By embracing these tools, the construction industry can enhance efficiency, reduce risks, and ultimately contribute to the longevity and success of concrete structures.
Future Developments In Concrete Drying
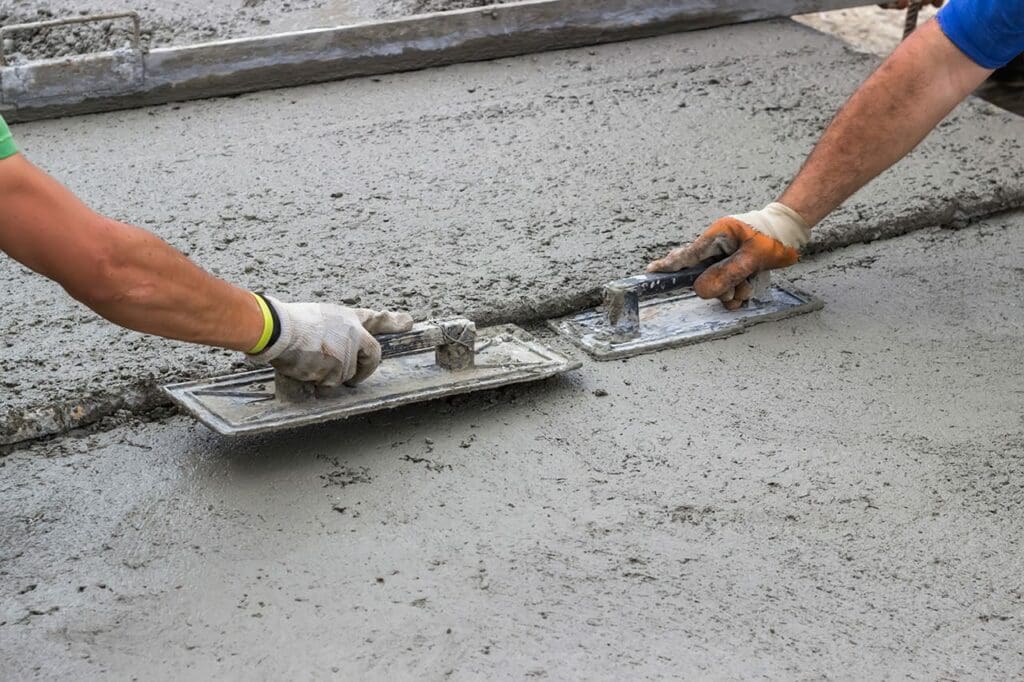
Concrete, the cornerstone of construction, is undergoing a transformative journey, and its drying process is no exception. As we look ahead, a wave of advancements promises to redefine how we approach concrete drying, enhancing efficiency, sustainability, and performance.
- Bright Concrete Mixtures: Innovations in concrete mix design are steering towards bright compositions that actively respond to environmental conditions. These mixes, equipped with sensors and additives, can adapt their drying rates based on real-time data, promising more precise control over the process.
- Self-Healing Concrete: Future concrete formulations may incorporate self-healing properties, mending microcracks naturally occurring during drying. This enhances durability and reduces the need for extensive maintenance over the lifespan of structures.
- Nanotechnology Integration: Nanoparticles are poised to play a pivotal role in the future of concrete drying. These tiny structures can modify the material at the molecular level, influencing the drying process and overall strength. The application of nanotechnology can revolutionize how we perceive and execute concrete drying.
- Sustainable Drying Methods: As sustainability takes centre stage in construction practices, future developments in concrete drying will prioritize eco-friendly methods. This includes exploring renewable energy sources for heating, implementing recycled water for curing, and developing drying techniques with a reduced carbon footprint.
- Real-Time Monitoring and Data Analytics: Advanced monitoring systems and data analytics will become integral to the concrete drying process. Real-time data on ambient conditions, moisture levels, and curing stages will empower construction professionals to make informed decisions, ensuring optimal drying results.
- 3D Printing and Prefabrication: The rise of 3D printing and prefabrication techniques will influence how concrete structures are built and dried. These methods offer controlled environments for drying, minimizing the impact of external factors and potentially accelerating the overall construction timeline.
- Climate-Adaptive Drying Strategies: Concrete drying strategies must adapt to climate change, affecting weather patterns. Future developments may include climate-responsive drying algorithms that adjust drying times based on anticipated weather conditions, ensuring consistency and quality.
The future of concrete drying is a landscape of innovation and sustainable practices. As research and technology converge, construction professionals can anticipate a paradigm shift approaching this critical building phase. Embracing these developments enhances the efficiency of construction projects and contributes to a more resilient and sustainable built environment. Stay tuned as we witness the evolution of concrete drying, shaping the construction industry’s future.
Final Words
A concise recap underscores the multifaceted aspects of concrete drying, emphasizing its pivotal role in ensuring structural integrity. The significance of proper concrete drying must be balanced, influencing strength, durability, and overall project success. As we conclude, the call to action echoes: let’s champion ongoing research and advancements in this field, fostering a future where innovative solutions continue to elevate construction practices, ensuring that concrete drying remains a cornerstone of resilient and sustainable building projects.