Die grinders and angle grinders are both powerful and versatile tools utilized across various industries for tasks such as cutting, grinding, and polishing diverse materials. Though they share similarities in purpose, these two types of grinders exhibit fundamental differences that are crucial to understanding when selecting the right tool for a particular job. This comprehensive guide aims to elucidate these differences and outline the biggest contrasts and similarities between die grinders and angle grinders, assisting users in making an informed choice.
Design:
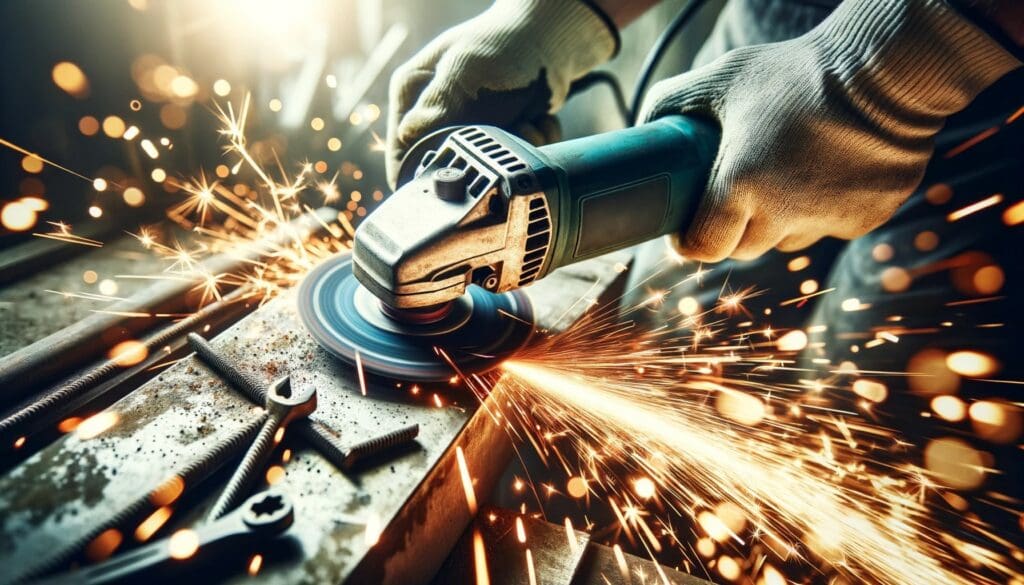
Die grinders boast a compact, straight, and cylindrical design, embodying the epitome of precision and ergonomics. They are handheld tools designed to be wielded with both hands, ensuring steady control during operation. This design is particularly advantageous for precision work in tight and confined spaces where meticulous attention to detail is paramount. On the flip side, angle grinders present a larger, more robust, and angular design. Typically held with one hand, these grinders feature an additional handle to provide users with enhanced control, especially during larger-scale tasks that demand stability.
In terms of the tool’s head, die grinders usually have a collet for attaching various bits and burs, while angle grinders possess a spindle to which a myriad of discs can be affixed. This distinction in design translates to different user experiences and capabilities, with die grinders offering more precision and angle grinders providing more brute strength.
Size:
Size plays a pivotal role in distinguishing between die grinders and angle grinders. Die grinders are inherently smaller, more compact, and lightweight, allowing for superior manoeuvrability and access to tight, hard-to-reach areas. Their small size is a boon for precision work and detailed tasks, making them a favourite among mechanics, artisans, and craftsmen.
Conversely, angle grinders are larger, heavier, and built for endurance, making them more suitable for heavy-duty jobs that demand substantial power and durability. Their size enables them to accommodate larger discs and attachments, broadening their application capabilities and making them a versatile tool in the arsenal of construction workers, welders, and DIY enthusiasts.
Power:
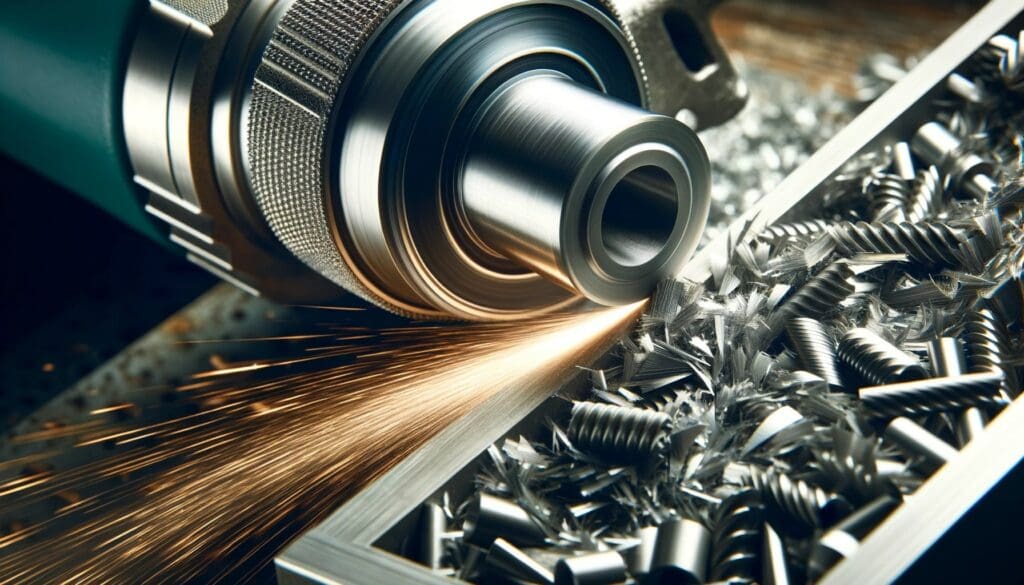
When it comes to power sources, die grinders offer versatility, available in both electric and pneumatic variants. Electric die grinders require a power outlet and come with a power cord, whereas pneumatic die grinders rely on air compressors and are connected via an air hose. Pneumatic die grinders tend to be lighter and offer a smoother operation due to the lack of internal motors, making them a preferred choice for prolonged use.
Angle grinders, predominantly electric, boast more powerful motors compared to their die grinder counterparts. This additional power makes them capable of handling larger amounts of material removal and tackling tough materials such as metal and concrete with ease. Some models of angle grinders also offer battery-powered variants, providing users with cordless convenience at the cost of some power.
Speed:
The speed at which these tools operate is another significant differentiator. Die grinders often feature higher speed ratings, operating at RPMs (revolutions per minute) ranging anywhere from 15,000 to 30,000 or even higher. This high-speed operation makes them ideal for tasks requiring precision, finesse, and a gentle touch, such as engraving, polishing, and finishing work.
In contrast, angle grinders typically operate at lower RPMs, ranging from 5,000 to 11,000, but compensate with higher torque. This slower, more powerful rotation is perfectly suited for heavy-duty tasks such as cutting through thick materials, grinding down surfaces, and other applications where raw power is necessary.
Application Capabilities:
Die grinders excel in precision tasks, shining in scenarios that demand work in tight spaces and intricate detailing. Their compact design and high-speed operation make them perfect for grinding, polishing, sanding, and carving in small and hard-to-reach areas. Mechanics often utilize die grinders for cylinder head porting, artisans for intricate carving, and welders for smoothing out welds.
Angle grinders, with their versatile nature, are well-equipped to handle a wide array of tasks across different materials. Their ability to accommodate various discs and attachments makes them suitable for cutting through materials like metal and stone, grinding down surfaces, and polishing flat areas. Construction workers commonly use them for cutting rebar and concrete, while metalworkers may use them for deburring and rust removal.
Key Differences Between Die Grinders and Angle Grinders
The most significant differences between die grinders and angle grinders lie in their design, size, power, and speed capabilities. Die grinders are smaller, designed for precision, and operate at higher speeds, making them ideal for detailed tasks in tight spaces. Angle grinders are larger, more powerful, and have a slower operation speed, making them suitable for heavy-duty tasks and larger surface areas.
Choosing the Right Tool for the Job
Understanding the unique characteristics of die grinders and angle grinders is crucial when choosing the right tool for a specific task. For precision work, detailed tasks, and operations in tight spaces, die grinders are the preferred choice. For larger-scale, heavy-duty tasks that require more power and durability, angle grinders are the ideal option.
Final Words
In summary, while both die grinders and angle grinders are indispensable tools in their own right, their differences in design, size, power, speed, and application capabilities set them apart, making them each uniquely suited for specific tasks. Die grinders, with their compact size and high-speed operation, are ideal for precision work in tight spaces. In contrast, angle grinders, being larger and more powerful, excel in heavy-duty tasks and working on flat surfaces. Understanding these characteristics ensures that users can make an educated decision, selecting the right tool for their specific needs and guaranteeing optimal performance and efficiency in their projects.